Difference between revisions of "Inspection and Maintenance: Green Roofs"
Line 132: | Line 132: | ||
|- | |- | ||
|colspan="7" style="text-align: center;" |'''<u><span title=>Note:''' (x) denotes indicators to be used for Performance Verification inspections only (i.e., not for Maintenance Verification inspections) </span></u> | |colspan="7" style="text-align: center;" |'''<u><span title=>Note:''' (x) denotes indicators to be used for Performance Verification inspections only (i.e., not for Maintenance Verification inspections) </span></u> | ||
|- | |||
|} | |||
==Construction Inspection Tasks== | |||
Construction inspections take place during several points in the construction sequence, specific to the type of LID BMP, but at a minimum should be done '''weekly''' and include the following: | |||
# During site preparation, prior to BMP installation to ensure the roof structure is ready for green roof construction work and confirm that BMP layout area matches approved design drawings and that construction materials meet design specifications | |||
# After installation of leak detection system (if applicable) to ensure it was done properly | |||
# At installation of water-proofing membrane, prior to installation of root barrier, drainage layer and overflow outlets to ensure it was done properly and to confirm that slopes are acceptable | |||
# After installation of root barrier, drainage layer (including filter fabric/layer) and overflow outlets, prior to installation of growing medium and plants to ensure it was done properly and confirm that depth and slopes are acceptable | |||
# After installation of growing medium layer and plants to ensure it was done properly and to confirm depth, slopes and elevations at overflow outlets are acceptable; After installation of irrigation system to confirm system is functioning | |||
# Prior to hand-off points in the construction sequence when the contractor responsible for the work changes (i.e., hand-offs between the building and green roof installation contractors) | |||
# After every large storm event (e.g., 15 mm rainfall depth or greater) to ensure roof drainage or flow diversion devices are functioning and adequately maintained. You can also download and print the table [https://wikidev.sustainabletechnologies.ca/images/6/6b/LID-IM-Guide-7.6-Green-Roofs.pdf '''here''']<br> | |||
</br> | |||
[[File:MaintenancePICP.png|thumb|400px|A Vacuum Truck used for [[permeable pavement]] maintenance, which sucks up excess sediment and fines trapped between the pores of block pavers. Conducting this maintenance regularly helps maintain the practice's optimal infiltration rate during large rain events. (Source: STEP).]] | |||
{| class="wikitable" style="width: 800px;" | |||
|+'''Permeable Pavements: Green Roofs''' | |||
|- | |||
!<br>'''Construction Sequence Step & Timing''' | |||
!<br>'''Inspection Item'''<br> | |||
!<br>'''<u><span title="Note for Observation Column: S = Satisfactory; U= Unsatisfactory; NA = Not Applicable ">Observations*</u>'''<br> | |||
|- | |||
|rowspan="6"|'''Site Preparation''' - after site clearing and grading, prior to BMP excavation and grading | |||
|Natural heritage system and tree protection areas remain fenced off | |||
| | |||
|- | |||
|ESCs protecting BMP layout area are installed properly | |||
| | |||
|- | |||
|CDA is stabilized or runoff is diverted around BMP layout area | |||
| | |||
|- | |||
|BMP layout area has been cleared and is staked/delineated | |||
| | |||
|- | |||
|Benchmark elevation(s) are established nearby | |||
| | |||
|- | |||
|Construction materials have been confirmed to meet design specifications | |||
| | |||
|- | |||
|rowspan="2"|'''BMP Excavation and Grading''' - prior to backfilling and installation of pipes/catchbasins | |||
|Excavated soil is stockpiled outside the CDA | |||
| | |||
|- | |||
|Excavation location, footprint, depth and slope are acceptable | |||
| | |||
|- | |||
|rowspan="6"|'''BMP Installation''' – after installation of pipes/catchbasins, prior to completion of backfilling | |||
|Structural components (e.g., pavement base, curbs) installation is acceptable | |||
| | |||
|- | |||
|Impermeable liner installed correctly, if applicable | |||
| | |||
|- | |||
|Installations of sub-drain pipes (e.g., locations, elevations, slopes), standpipes/monitoring wells are acceptable | |||
| | |||
|- | |||
|Sub-drain trench dams installed correctly (location, elevation) | |||
| | |||
|- | |||
|Surface coarse installation (elevation, slope, monitoring wells) is acceptable | |||
| | |||
|- | |- | ||
|} | |} |
Revision as of 14:29, 8 August 2022
Overview[edit]
Green roofs are engineered rooftop design features that allow the growth of vegetation on rooftops and have numerous benefits. These LID BMPs can also be referred to as vegetated roofs, rooftop gardens or eco-roofs. A green roof acts like a lawn, meadow or garden by intercepting and absorbing a portion of the rainwater or snowmelt that falls on it. The typical layers of a green roof (in ascending order from the roof surface) include a water-proofing membrane, drainage layer, lightweight growing media layer and the vegetation. Excess water that is not absorbed by the growing media or vegetation is collected by the underlying drainage layer, directed to outlet structures and conveyed via the roof drainage system to another BMP or the municipal storm sewer system. A portion of the water absorbed by green roofs is returned to the atmosphere by evaporation and transpiration by plants. Green roofs are typically designed to retain precipitation from small to medium-sized (e.g., 5 to 25 mm rainfall depth) storm events. Overflow outlets are necessary to safely convey flows from major storm events.
Some of the benefits of green roofs include:
- The ability to reduce the quantity of pollutants and runoff being discharged to municipal storm sewers and receiving waters (i.e., rivers, lakes and wetlands);
- Growing media and plants retain pollutants deposited from the atmosphere and reduce metals and other pollutants from conventional roof materials transported by runoff;
- Improve the energy efficiency of the building due to their insulating properties;
- Reduce the urban heat island effect;
- Can provide food and shelter for pollinators;
- Can provide aesthetic value as attractive landscaped features.
Key components of Underground Infiltration Systems to pay close attention to are the:
Associated Practices[edit]
- Intensive green roofs contain greater than 15 cm depth of growing media, can be planted with deeply rooted plants (e.g., shrubs and trees) and can be designed to handle pedestrian traffic.
- Extensive green roofs consist of a thinner growing media layer (15 cm depth or less) and are typically planted with.
- Blue roofs are systems that temporarily capture rainwater using the roof as storage and allow it to evaporate and/or to be used for non-potable requirements (i.e. irrigation, toilet flushing, truck washing) and ultimately offset potable water demands.
Inspection and Testing Framework[edit]
Component |
Indicators |
Construction Inspection |
Assumption Inspection |
Routine Operation Inspection |
Verification Inspection |
---|---|---|---|---|---|
Perimeter | |||||
BMP dimensions | x | x | x | ||
Growing medium/filter bed | |||||
Green roof structural integrity | x | x | x | ||
Standing water | x | x | x | ||
Filter bed erosion | x | x | |||
Vegetation | |||||
Vegetation cover | x | x | x | x | |
Vegetation condition | x | x | |||
Vegetation composition | x | x | x | ||
Overflow outlets | |||||
Overflow outlet obstruction | x | x | x | x |
Component |
Indicators |
Construction Inspection |
Assumption Inspection |
Routine Operation Inspection |
Verification Inspection | |
---|---|---|---|---|---|---|
Testing Indicators | ||||||
Soil characterization testing | x | x | (x) | |||
Green roof irrigation system testing | x | x | x | |||
Green roof leak detection testing | x | x | ||||
Note: (x) denotes indicators to be used for Performance Verification inspections only (i.e., not for Maintenance Verification inspections) |
Construction Inspection Tasks[edit]
Construction inspections take place during several points in the construction sequence, specific to the type of LID BMP, but at a minimum should be done weekly and include the following:
- During site preparation, prior to BMP installation to ensure the roof structure is ready for green roof construction work and confirm that BMP layout area matches approved design drawings and that construction materials meet design specifications
- After installation of leak detection system (if applicable) to ensure it was done properly
- At installation of water-proofing membrane, prior to installation of root barrier, drainage layer and overflow outlets to ensure it was done properly and to confirm that slopes are acceptable
- After installation of root barrier, drainage layer (including filter fabric/layer) and overflow outlets, prior to installation of growing medium and plants to ensure it was done properly and confirm that depth and slopes are acceptable
- After installation of growing medium layer and plants to ensure it was done properly and to confirm depth, slopes and elevations at overflow outlets are acceptable; After installation of irrigation system to confirm system is functioning
- Prior to hand-off points in the construction sequence when the contractor responsible for the work changes (i.e., hand-offs between the building and green roof installation contractors)
- After every large storm event (e.g., 15 mm rainfall depth or greater) to ensure roof drainage or flow diversion devices are functioning and adequately maintained. You can also download and print the table here
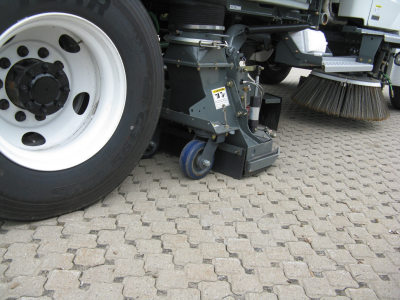
Construction Sequence Step & Timing |
Inspection Item |
Observations* |
---|---|---|
Site Preparation - after site clearing and grading, prior to BMP excavation and grading | Natural heritage system and tree protection areas remain fenced off | |
ESCs protecting BMP layout area are installed properly | ||
CDA is stabilized or runoff is diverted around BMP layout area | ||
BMP layout area has been cleared and is staked/delineated | ||
Benchmark elevation(s) are established nearby | ||
Construction materials have been confirmed to meet design specifications | ||
BMP Excavation and Grading - prior to backfilling and installation of pipes/catchbasins | Excavated soil is stockpiled outside the CDA | |
Excavation location, footprint, depth and slope are acceptable | ||
BMP Installation – after installation of pipes/catchbasins, prior to completion of backfilling | Structural components (e.g., pavement base, curbs) installation is acceptable | |
Impermeable liner installed correctly, if applicable | ||
Installations of sub-drain pipes (e.g., locations, elevations, slopes), standpipes/monitoring wells are acceptable | ||
Sub-drain trench dams installed correctly (location, elevation) | ||
Surface coarse installation (elevation, slope, monitoring wells) is acceptable |
- ↑ Jump up to: 1.0 1.1 1.2 TRCA. 2018. Fact Sheet - Inspection and Maintenance of Stormwater Best Management Practices: Green Roofs. https://sustainabletechnologies.ca/app/uploads/2018/02/Green-Roofs-Fact-Sheet.pdf