Difference between revisions of "Rainwater Harvesting Cistern: Life Cycle Costs"
(Created page with "|thumb|500px|[[Enhanced swale with rocky check dams and a metal overflow grate in Northgate Mall parking lot, Seattle. Photo credit: MLSmith.]] {{TOClimit|2}} ==Overview== Rainwater harvesting is the process of intercepting, conveying and storing rainfall for future use. The term “rainwater harvesting” (RWH) is used herein to refer to capturing rainfall onto rooftops (i.e. “roofwater”) and stormwater...") |
(No difference)
|
Revision as of 19:53, 20 December 2022
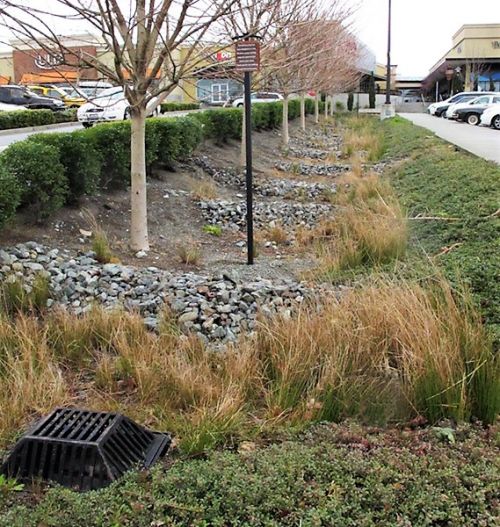
Overview[edit]
Rainwater harvesting is the process of intercepting, conveying and storing rainfall for future use. The term “rainwater harvesting” (RWH) is used herein to refer to capturing rainfall onto rooftops (i.e. “roofwater”) and stormwater runoff from the ground surface (i.e. “stormwater”), and then reusing for irrigation or other greywater-approved uses. The rain that falls upon a catchment surface, such as a roof, is collected and conveyed into a storage facility. Storage tanks, a common method for storage, range in size from rain barrels for residential land uses (typically 190 to 400 litres in size), to large cisterns for industrial, commercial and institutional land uses. A typical pre-fabricated cistern can range from 750 to 40,000 litres in size. STEP has prepared life cycle costs estimates for each design configuration, based on a 2,000 m2 road drainage area, runoff control target of 25 mm depth and 72 hour drainage period, for comparison which can be viewed below. To generate your own life cycle cost estimates customized to the development context, design criteria, and constraints applicable to your site, access the updated LID Life Cycle Costing Tool (LCCT) here.
Design Assumptions[edit]
Rainwater harvesting (RWH) is ideal for sites that cannot infiltrate water (e.g. contaminated soils, WHPAs, IPZs, etc.), zero-lot-line developments, extensive gardens and landscapes. Components include: catchment area (e.g. rooftop), filter to remove coarse debris, cistern storage, and a connecting pipe network. Additional components include pumps to lift water to higher elevations, additional water filtration and treatment.
Design and operation and maintenance program assumptions used to generate cost estimates are based on tool default values and the following STEP recommendations:
- Native soil infiltration rates for Full, Partial and No Infiltration Design scenarios were assumed to be 20 mm/h, 10 mm/h and 2 mm/h, respectively, and a safety factor of 2.5 was applied to calculate the design infiltration rate.
- Operation and maintenance (O&M) cost estimates assume annual inspections, removal of trash and debris twice a year, removal of sediment from pretreatment structures annually, and removal of weeds twice a year (where applicable). Verification inspections are included every 5 years to confirm adequate maintenance, and every 15 years to confirm adequate drainage performance through in-situ surface infiltration rate testing (where applicable)
- Can be used throughout the year if they are located underground or indoors to prevent problems associated with freezing.
- Separate plumbing, pumps, pressure tanks, and backflow preventers are necessary for indoor use of harvested water.
- Back-up water supply system arrangements, that can be drawn upon when the cistern runs dry , are also necessary for indoor uses.
- Storage tanks in low elevated areas will increase volume of rainwater stored, but will increase the amount of pumping needed to distribute water.
- The opposite occurs for placing tanks at higher elevations.
- Cisterns should be placed on or in native, rather than fill, soils.
- Underground tanks and piping to and from cisterns should either be located below the local frost penetration depth or insulated to prevent freezing.
- An underdrain (minimum 200 mm perforated pipe) is only needed when native soil infiltration is less than 15 mm/hr or infiltration is precluded.
- Overflow devices should be designed to avoid causing ponding or soil saturation within 3 metres of building foundations.
- Tanks must be watertight to prevent water damage when placed near building foundations.
- Pretreatment is needed to remove debris, dust, leaves, and other debris that accumulates on roofs and can cause clogging within the RWH system.
Notes[edit]
- Overflow was not costed as it would be needed even if the RWH system was not constructed.
- Costs for conveyance piping are not included in the model design for indoor tanks because conveyance would be needed even without RWH.
- The cost for decommissioning an outdoor above-ground plastic tank for the winter is not included.
- The tool assumes that only one trench is needed for all piping, including conveyance, service and top-up piping.
- The tool calculates costs for new (greenfield) development contexts and includes costs for contractor overhead and profit, material, delivery, labour, equipment (rental, operating and operator costs), hauling and disposal.
- Land value and equipment mobilization and demobilization costs are not included, assuming BMP construction is part of overall development site construction.
- Design and Engineering cost estimates are not calculated by the tool and must be supplied by the user.
- The tool adds 10% contingency and additional overhead as default.
- All cost estimates are in Canadian dollars and represent the net present value (NPV) as the tool takes into account average annual interest and discount rates over the 25 and 50 year operating life cycle periods.
- Unit costs are based on 2018 RSMeans standard union pricing.
- Additional costs associated with retrofit or redevelopment contexts is assumed to be 16% of the cost estimate for new (greenfield) construction contexts.
- Retrofit construction cost estimates are included in the 'Costs Summary' section for comparison.
- Retrofit construction cost estimates are included in the 'Costs Summary' section for comparison.
Construction Costs[edit]
Note: Please click on each image to enlarge to view associated construction cost estimates.
Above you can find a cost breakdown of a 1000m2 in two different configurations:
As can be seen, regardless of design configuration, Material & Installation expenses represent the largest portion of total construction costs (50%).
Life Cycle Costs[edit]
Below are capital and life cycle cost estimates for the Enhanced swales Full Infiltration configuration over 25- and 50-year time periods. The estimates of maintenance and rehabilitation (life cycle) costs represent net present values. Operation and maintenance costs are predicted to represent 45% of total life cycle costs over the 25-year evaluation period, and increase to 59% of total life cycle costs over the 50-year period, due to increased levels of litter removal, watering (establishment period - years 1 & 2 / annually and / drought watering) cleaning out and vacuuming of the catchbasin, mowing, replacement of sod, weeding and pruning of the BMP's planted vegetation.
25-Year life cycle cost break down[edit]
Note: Click on each image to enlarge to view associated life cycle cost estimate.
50-Year life cycle cost break down[edit]
Note: Click on each image to enlarge to view associated life cycle cost estimate.
Cost Summary Tables[edit]
Total life cycle cost estimates for the Enhanced swale Full Infiltration design configuration is ($23,451.36), makign it one of the cheapest LID BMP options.
It is notable that a sensitivity analysis was conducted in 2019 to compare construction cost estimates generated by the tool to actual costs of implemented projects. The analysis found that tool estimates were typically within ±14% of actual construction costs[1]
Full Infiltration[edit]
References[edit]
- ↑ Credit Vally Conservation (CVC). 2019. Life-cycle costing tool 2019 update: sensitivity analysis. Credit Valley Conservation, Mississauga, Ontario. https://sustainabletechnologies.ca/app/uploads/2020/04/LCCT-Sensitivity-Analysis_March2020.pdf